Angled gear units: The agony of choice – bevel gear or worm
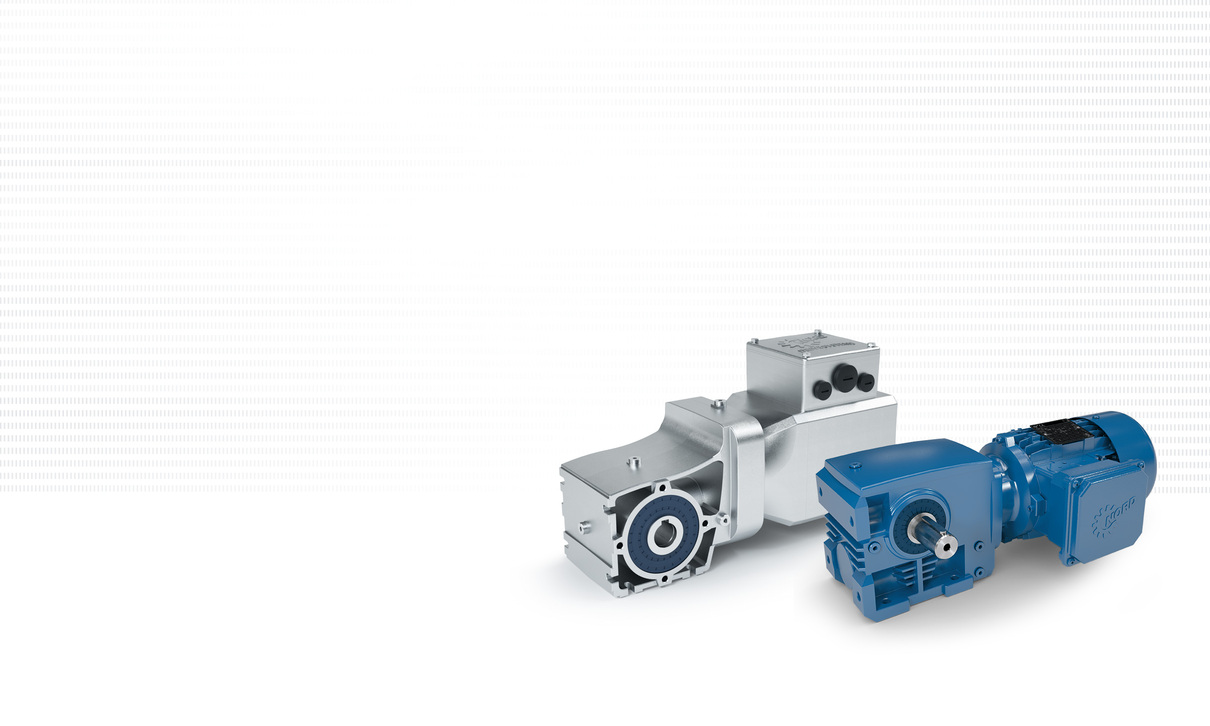
Right angled gear units are the solution for applications in which the input shaft and output shaft must be arranged at an angle – usually a right angle – for example in confined installation spaces. The axes can intersect or cross with an axle offset. In the industrial sector, right angled gear units are mainly designed as bevel or worm gear units. In the following, we will explain when to use which of these two gear unit types.

Right angled gear units are often used to fit a geared motor into the available installation space in a space-saving manner. This is often the case with conveyor belts and travelling drives (aisle width), for example. Possible gear drive designs for right angled gear units:
- Bevel gear unit
- Worm gear units
- Hypoid gear units
- Spiroplan gear units (spiroid gearing)
- Screw gear units
- Crown gear units
Hypoid gear units, spiroplan gear units and crown gear units can be regarded as modifications of bevel gear units, and screw gear units as modifications of worm gear units. Same as worm gear units, hypoid gear units, spiroplan gear units and screw gear units do not have intersecting but offset axes. With increasing axle offset, the slippage in the gearing and the demand on the lubricants to prevent fretting increases.
The most commonly used angled gear units in the industrial sector are bevel gear units and worm gear units. We will therefore concentrate on these two gear unit types in the following. With right angled gear units at least one gear stage must realise the angular position of the axes. This gear stage is then designed as a bevel gear or worm gear stage.
Complex design
Due to the intersecting or crossed axes that often also have to be set and held in a precise axial position, angled gear units have a complex design. This is required so that the power is transmitted to the tooth flanks via large, centred wear patterns. Another difficulty is the fact that the gearing itself exerts axial forces on the axes. Therefore, axially preloaded conical roller bearings are often used for bevel gear units.

Design of worm gear units
Worm gear units consist of a helical worm shaft and a worm wheel (gearwheel).</904> In conventional cylindrical worm gear units, the worm is cylindrical and does not require axial adjustment during assembly. The worm wheel has a globoidal shape to ensure a wide wear pattern. For globoid worm gear units, the opposite is true.
The worm shaft rotates faster than the worm wheel, whereby the ratio of the number of worm wheel teeth to the number of worm teeth represents the speed ratio and thus the ratio of the worm gear stage. A worm gear stage always has an offset of the intersecting axes. This is referred to as centre distance and indicates the size. This offset allows both the worm shafts and worm wheel shafts to be continuous in (single-stage) worm gear units which sometimes proves to be advantageous in terms of design compared to bevel gear units. The helical motion sequence with its high slippage in the sliding rolling contact of the gear meshing means that seizure-proof materials such as bronze are used as worm wheel materials.

Design of bevel gear units
A bevel gear stage consists of a bevel pinion and bevel gear (often called crown wheel). They can be straight-toothed, helicaltoothed or spiral-toothed. Nowadays, both the bevel pinion and the crown wheel are usually made of case-hardened steel, which means that they can be operated almost wear-free with good lubrication.
In its simplest form, a bevel gear unit consists of only one gear stage. However, NORD bevel gear units always have several gear stages: Except for industrial gear units, our stage arrangement is as follows:
- 2-stage: Helical gear stage (first stage), bevel gear stage (second stage)
- 3-stage: Helical gear stage (first stage), bevel gear stage (second stage), helical gear stage (third stage)
- 4-stage: Helical gear stage (first stage), helical gear stage (second stage), bevel gear stage (third stage), helical gear stage (fourth stage)
Advantages of worm gear units
Due to the high sliding component in the gear meshing, the noise emission of worm gear units is very low, and the speed ratio range of a worm gear stage is very large in practice (approx. i = 4 to 100). This often requires fewer gear stages, which reduces the number of moving parts, the size, the weight, the costs and also the load-independent power losses. Since a larger number of worm gear teeth are in mesh at the same time, worm gear units can withstand high overloads and shocks for short periods without damage. The advantages of these gear units are particularly evident in intermittent operation (e.g. actuator drives), in applications with shocks and load ranges with greatly varying loads and with longer running times in the low-load range, as well as in small sizes. Worm gear units can be self-locking when the power flow is reversed with certain toothing designs, which means that brakes can be selected to be smaller or omitted entirely.
Disadvantages of worm gear units
Due to the high sliding component, worm gear stages with a high ratio (approx. i > 10) have a lower efficiency compared to the gearing of bevel gear stages. Furthermore, the static friction in the gearing must be overcome when starting up under load. These effects must be taken into account in the motor design, particularly with higher ratios in the worm gear unit. Bronze, which is often used due to the high sliding, has the disadvantage that its alloy components are very expensive to purchase. Applications with a high number of operating hours (e.g. continuous operation) under prolonged high loads can lead to wear of the bronze worm wheel and thus limit the service life.
Advantages of bevel gear units
Due to the high proportion of rolling during gear meshing, the efficiency of the gearing is high. The bevel gear stage can also realise speed ratios of 1:1 with high efficiencies of 96 to 98%. By turning the crown wheel, the direction of rotation can be changed with the same gear components if there is enough space in the gear unit housing. Bevel gear units are preferably used in applications with a high number of operating hours (e.g. continuous operation), prolonged high loads or constant operation.
Disadvantages of bevel gear units
Due to the high proportion of rolling and the small tooth overlap in the gearing, the noise emission of bevel gear units is higher than that of worm gear units. The practical maximum ratio of a bevel gear stage is also limited to i = 6, because otherwise the load capacity would be reduced too much for a given size. This means that additional gear stages (usually helical gear stages) are required for higher desired ratios, which increases the installation space, weight, number of parts and costs. Due to the mostly overhung bevel pinion arrangement and to ensure good load carrying in the gear meshing, the bevel pinion and crown wheel must be precisely aligned axially. This requires large, load-bearing bearings. Preloaded conical roller bearing arrangements with high bearing friction are very often selected because they best fulfil the bearing capacity requirements. Due to the higher number of gear stages and the preloaded bearings, the load-independent power losses are often higher than with worm gear units which means that the efficiency in the partial load range drops significantly, particularly with small sizes.
Wide product range from NORD
NORD has a wide range of products: Depending on the application, we can supply both bevel gear units and worm gear units and are therefore unbiased in our selection. This enables us to offer the optimum solution for every application. The torque range of the NORD angled gear units ranges from approx. 20 to 280,000 Nm!
Right angled gear unit solutions from NORD are characterised by the fact that our variety allows us to provide an optimum solution from our modular system in most cases, even for small quantities. In the area of small worm gear units for example, NORD has a very large, proven, modular system, which makes it easy to find good solutions for many applications. For large belt drive units, which NORD implements with industrial gear units on swing bases, worm gear units are out of the question due to their size and the power required. These would have a heat problem in these sizes.

For high ratio requirements: Worm gear units from NORD
NORD worm gear units are optimally suited for use in intralogistics, packaging technology or the food industry. In addition to the high ratio requirements, this is due to the high peak loads that sporadically occur in these areas as well as the long running times at low loads. Furthermore, our worm gear units can be operated with food-grade lubricants. Worm gear units also offer many advantages for bread slicers in bakeries or supermarkets, as they can withstand the hard impacts that occur when starting up, braking and plunging the blade into the bread. The quiet running is also very advantageous for these applications. Worm gear units are also often used as drives for elevators in buildings due to their quiet running, intermittent operation and self-locking.
When using worm gear units, it should be taken into account that the gear unit supports the brake in generator mode, e.g. when braking masses. Due to the temporary efficiency reduction during a power flow reversal, brakes can and should therefore be dimensioned smaller. In the high ratio range, it may even happen that worm gear units in the worm gear stage can be self-locking at standstill or even self-braking when running. Depending on the application, this property can be damaging or beneficial. With actuator drives, for example, once a position has been reached, it can be held even without a brake. Self-braking can also be damaging, e.g. in the form of chatter vibrations during load reductions in generator mode. NORD has developed its own calculation tool for this purpose and can take these properties into account when selecting the drive.
Three good reasons for our solutions:
- Robust: Our worm gear motors have a high overload capacity.
- User friendly: Wash-down versions enable simple and efficient cleaning of the drive systems.
- Flexible: Our modular components give users maximum freedom.

Modular system for maximum flexibility
There are countless applications for drive systems, and each of these has its own specific requirements. With the SI series UNIVERSAL worm gear motors, all components can be combined as required for the application. UNIVERSAL worm gear units impress with their high power density and low space requirements.
A clean affair
Especially in hygienically sensitive industries such as the food or pharmaceutical industries, plant and components must be easy to clean. Because of this, our SMI series UNIVERSAL worm gear motors have a smooth surface. These geared motors are optionally supplied with IEC or NEMA motor or with direct coupling-free motor mounting in flange or foot-mounted versions.
Compact and efficient
The die cast aluminium UNICASE housing of the two-stage helical worm gear unit SK 02040.1 ensures maximum strength and rigidity with low weight. The gear unit covers a power range from 0.12 to 1.10 kW and torques up to 100 Nm. The wide range of speed ratios from 5.37:1 up to 330:1 enables optimum adaptation to the customer's requirements.

Bevel geared motors from NORD
Our drive systems, consisting of an electric motor and a bevel gear unit, are especially suitable for use on conveyor belts as well as in intralogistics, packaging technology and the food industry. The advantages of our bevel geared motors:
The classic
The UNICASE bevel geared motor provides a torque range from 180 to 50,000 Nm and takes up little installation space thanks to its compact UNICASE housing. Like all other NORD bevel geared motors the motor is available with an integrated back stop and integrated brake.
Even more power
With our NORDBLOC.1 drive systems with bevel gear units, we have optimised performance even further: They are now our most powerful bevel geared motors. As standard, we manufacture the NORDBLOC.1 motors with bevel gear units with a high strength die cast aluminium housing. We have developed our NORDBLOC.1 bevel geared motors from the series SK 930072.1 - SK 93772.1 especially for wash-down applications, e.g. in the food industry. This version has an especially smooth housing made of aluminium permanent mould castings, which is easy to clean and prevents the accumulation of dirt.
- Powerful: Torques of up to 50,000 Nm (as industrial geared motors up to 282,000 Nm)
- Efficient: Very high efficiency over the entire speed ratio range
- User friendly: The easy-to-clean wash-down version ensures Cleanliness (NORDBLOC.1®)
- Flexible: The direction of rotation between the input and output shaft can be easily reversed

Bevel geared motors for intralogistics
In combination with an IE4 synchronous motor, our 2-stage bevel gear units become the energy-efficient LogiDrive system for intralogistics. LogiDrive drive units have a large overload capacity and greatly reduce operating costs thanks to their high efficiency. Due to their modular structure, users also make considerable savings in maintenance costs.
The service-friendly and standardised modular system combines different NORD products into one drive solution, which is 100% tailored to the respective industry standards and application requirements. We differentiate between the sectors of post & parcel and airport on the one hand, and warehouse on the other. The first application area includes drives for parcel distribution and sorting systems as well as baggage handling, while the latter includes conventional warehouse applications such as pallet, container and overhead conveyors. In both areas, we offer a basic and advanced version.

Industrial gear units for maximum torques
High load capacities, high torques and low noise: NORD’sMAXXDRIVE right-angle gear units. With output torques of up to 260,000 Nm and powers of up to 4,000 kW, these gear units provide the necessary drive in heavy-duty applications such as conveyor belt systems, mixers, agitators, extruders, drums or mills. The right-angle gear units are available as 2-stage, 3-stage and 4-stage versions. Their gearwheels are made from high-quality steel alloys and are case-hardened. With our UNICASE housing, we can use larger roller bearings, which guarantee a long service life. Another advantage is that they can be easily installed on all six sides.
Would you like to discover more about angled gear units and the advantages for your application?