Cómo se fabrica un equipo descentralizado: un vistazo entre bambalinas en Aurich
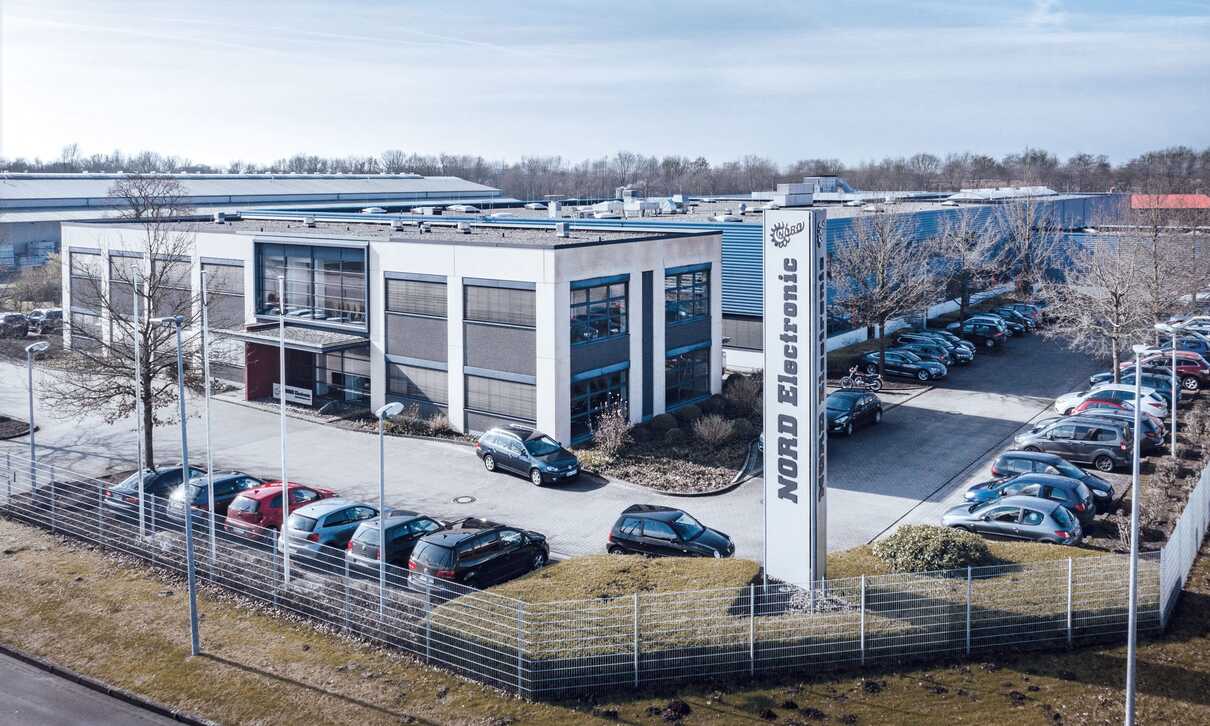
La era de la producción industrial en masa con pocas variantes del producto y grandes cantidades del mismo hace mucho que ha pasado. Hoy en día la individualidad está más demandada que nunca. Los clientes requieren cada vez más configuraciones específicas adaptadas con exactitud a sus necesidades individuales. Y esta tendencia global continuará ininterrumpida en el futuro. Al mismo tiempo se solicitarán lotes de producto cada vez más pequeños. Esta tendencia a cada vez más modelos con tamaños de lote cada vez más reducidos no puede gestionarse con las estructuras de fabricación convencionales. Por tanto, para poder reaccionar con rapidez y flexibilidad a los deseos de los clientes y a los cambios en el mercado, hacen falta procesos de fabricación inteligentes, versátiles y eficientes. La Industria 4.0, la producción inteligente completamente en red, es la respuesta a esto.
Tanto si acaban utilizándose en Europa como en China o los Estados Unidos de América, la cuna de todos los variadores de frecuencia de NORD, tanto los de instalación en el armario de distribución como los descentralizados, se encuentra en la planta que la empresa posee en Aurich, en Frisia Oriental. Desde comienzos de los años 80 del siglo pasado, NORD DRIVESYSTEMS, uno de los proveedores integrales de tecnología de accionamiento mecánica y electrónica líderes mundiales, gestiona su propia planta de fabricación de equipos electrónicos al noroeste de la Baja Sajonia. Con el transcurso de los años hemos ido ampliando constantemente tanto nuestra gama de productos como nuestra sede. Hoy, la sede de NORD Electronic DRIVESYSTEMS GmbH emplea a 180 trabajadores (más otros 40 previstos) y en 2022 salieron de la fábrica 185 000 unidades; y la tendencia sigue al alza. La superficie de producción ocupa 7000 m2 y la de oficinas 1300. La oferta incluye tecnología de accionamiento electrónica de hasta 160 kW (variadores, arrancadores de motor y electrónica). Para comenzar a producir los equipos descentralizados NORDAC LINK en serie, durante la ampliación de la planta entró en servicio una nueva línea de montaje.
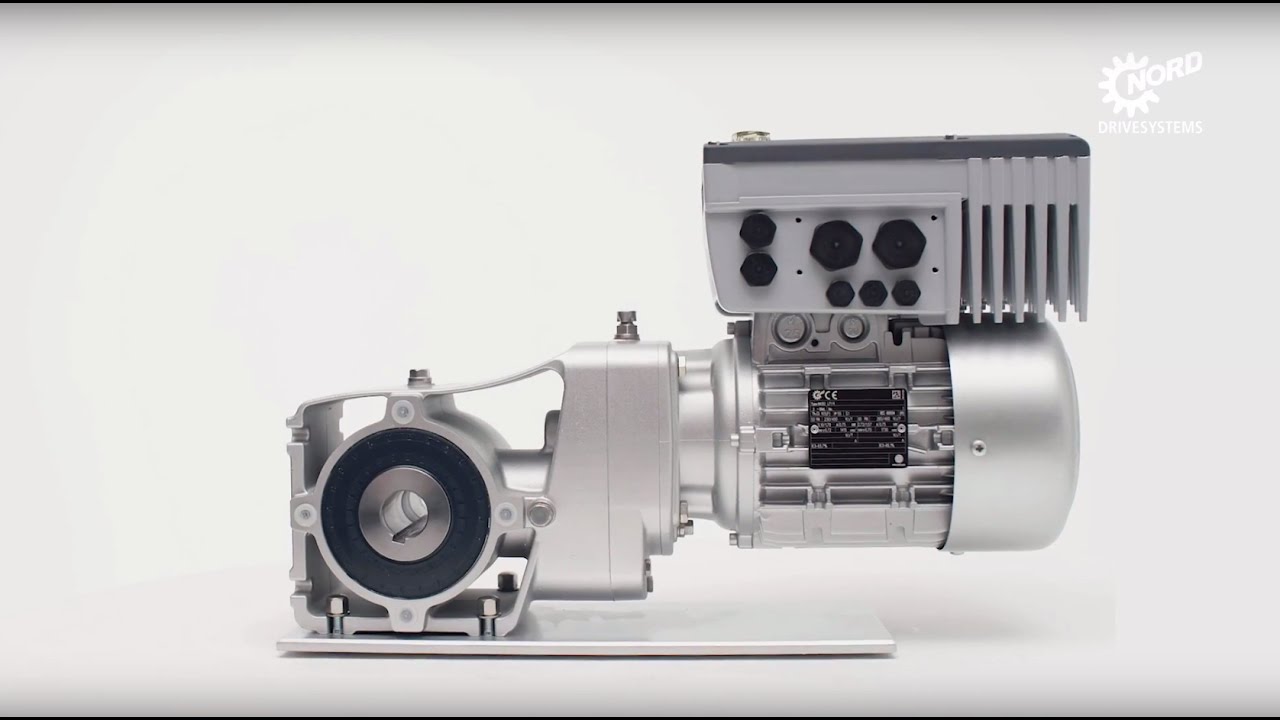
Asimismo, la última generación de variadores de frecuencia NORDAC PRO para montaje en armario de distribución también se fabrica en Aurich con tecnología y logística de fabricación vanguardista. Los últimos años se ha registrado, sobre todo, una elevada demanda de equipos de configuración individualizada. Por este motivo hemos seguido invirtiendo en la sede de Aurich y hemos logrado ampliar notablemente su capacidad, entre otros, gracias a una inversión de unos 2,5 millones de euros. La superficie para el montaje de los proyectos de nuestros clientes ha pasado a ocupar 3000 m2 distribuidos en dos pisos. La capacidad de fabricación actual es de 400 000 unidades, es decir, variadores de frecuencia de todos los tamaños. Y tras la adquisición de un solar adyacente con una superficie de 1,8 ha, nada nos va a impedir seguir ampliando la sede de Aurich en el futuro.
Logística ajustada – procesos eficientes
El avance de la digitalización, la flexibilización y la individualización de la industria fue el detonante que nos llevó a desarrollar el equipo descentralizado NORDAC LINK y a apostar rehiteradamente por una fabricación puntera de nuestra electrónica de accionamiento. La tendencia hacia los pedidos personalizados, los lotes de menor tamaño y los equipos descentralizados sigue al alza. La tecnología de accionamiento más moderna debe ser flexible e individualizable, y debe poder integrarse sin problema alguno en cualquier sistema. Nosotros nos enfrentamos a este desarrollo con el NORDAC LINK y, por descontado, con todas las otras series nuevas de variadores de frecuencia.
La serie se desarrolló especialmente en nuestras modernas instalaciones de logística interna en red y constituye una cómoda solución de accionamiento para la instalación flexible y descentralizada. Gracias al PLC integrado, los eficientes equipos descentralizados pueden asumir funciones de control y regulación del proceso integrales de forma autónoma. Todos los módulos, series y conexiones del NORDAC LINK se combinan mediante sencillos conectores rápidos. Además de la gran conectabilidad, el seccionador de mantenimiento y el interruptor de funcionamiento manual integrados, ambos opcionales, garantizan una elevada facilidad de manejo. El equipo descentralizado puede configurarse para cada aplicación y requisito, y es compatible con todos los sistemas bus convencionales. Con esto ofrece al cliente muchas más opciones de individualización que los productos con los que contábamos hasta ahora. Aunque esto, obviamente, ha repercutido en la fabricación. El objetivo a la hora de planificar los procesos de producción del NORDAC LINK era controlar todos los sistemas de montaje y ensayo necesarios a partir de la configuración individual. La implantación de esta estrategia fue todo un éxito, desde el esbozo del plan de montaje de las piezas hasta la comprobación final y la parametrización.
Desde la placa conductora hasta el equipo descentralizado terminado
La flexible estructura de producción automatizada en Aurich se encuentra a la vanguardia tecnológica, lo que nos permite ejecutar cualquier encargo de la misma forma, tenga la envergadura que tenga. La producción flexible permite incluso fabricar lotes pequeños. El NORDAC LINK se produce directamente por encargo del cliente. Se configura a nivel modular en SAP y después se equipa y monta en función de las especificaciones del pedido. Esto ofrece al cliente la posibilidad de configurar muchas más características. Y el propio proceso de producción también entraña ventajas, puesto que la fabricación se controla íntegramente a través de un pedido central. Todos los datos e información se recopilan online y pueden consultarse en cualquier momento y desde cualquier lugar. Así, entre otros, los planes de equipamiento y ensayo se generan automáticamente a partir de la configuración individual del cliente, tanto en el montaje THT como en el montaje SMD (Surface Mounted Device). Esto es una gran novedad en cuanto al equipamiento de módulos.
El proceso eficiente comienza ya desde la recepción de la mercancía. Para utilizar la menor cantidad de embalajes posible durante la producción, los productos que llegan en palés se extraen de su envoltorio y se trasladan a cajas estándar. A continuación, el FTS se encarga de transportarlos. Además, a la mercancía se le adjudica un código 2D, por lo que puede realizarse un seguimiento íntegro de la misma hasta que se utiliza o seguirse a la inversa, es decir, desde el número de serie del aparato hasta la recepción de mercancía.
El punto clave es el almacén automático de piezas pequeñas, que cuenta con más de 2000 espacios de almacenamiento estándar divididos en seis compartimentos y se ha integrado de manera centralizada en los procesos de producción. Además, sirve para almacenar tanto los componentes como los productos semiacabados y también para encadenar los procesos de producción. Después del área de montaje SMD, los módulos ya equipados vuelven al AAPP y se retiran del mismo para continuar con el montaje THT. Así es como se lleva a cabo un proceso FIFO (First in, First out) automático en un proceso de producción.
Si las dos líneas de equipamiento para el montaje SMD trabajan a pleno rendimiento, tienen una capacidad de 60 000 piezas por hora. Para garantizar una producción sin errores, después de equipar los módulos y soldarlos en atmósfera de nitrógeno, estos se inspeccionan con un sistema AOI (inspección óptica automática) en línea. Durante el montaje THT se instalan los componentes cableados y se sueldan con soldadura por onda en atmósfera de nitrógeno. En función de la complejidad, también se lleva a cabo una AOI del montaje THT y a continuación una prueba de funcionamiento integral. Después del montaje THT, el módulo pasa directamente al almacén Kanban de la fase de montaje final. Debido a que todos los productos se fabrican bajo pedido, es suficiente con una fase previa de producción más corta y menor capacidad de almacenamiento.
Nuestros equipos, como los reductores, los motores y los variadores, se fabrican en las distintas plantas de NORD y se envían a nuestra sede en Bargteheide para combinarlos y crear nuestras soluciones de accionamiento. En calidad de centro logístico, NORD DRIVESYSTEMS Bargteheide cuenta con más de 34 000 espacios de almacenaje, 17 000 de los cuales se encuentran en el almacén de estanterías altas. El nuevo almacén de piezas pequeñas, que cuenta con más de 70 000 espacios, se inauguró en 2021 y a día de hoy es el mayor sistema de almacenamiento automático del Grupo NORD DRIVESYSTEMS. Al lado del almacén automático de piezas pequeñas (AAPP) se han ubicado las nuevas naves, con 4400 puestos para palés y un área de recepción y envío de mercancía. Ahora, aquí también se encuentra la sección de embalaje de piezas. En el futuro, esto nos permitirá suministrar los variadores de frecuencia, unidades reductoras y motores a nuestros clientes y filiales con mayor celeridad. Además, debido a la elevada disponibilidad de los componentes, en la sede de Bargteheide se han reducido los plazos de montaje.
Descartar las fuentes de error, mantener los estándares de calidad
Antes de poner rumbo a la central técnica de accionamientos en el norte de Alemania, los variadores de frecuencia deben cumplir los elevados estándares de calidad que exige el mercado. Para garantizar su cumplimiento, en Aurich se han integrado controles de calidad en todos los niveles de fabricación. El proceso comienza con el control de las piezas en la recepción de mercancía y sigue durante el equipamiento de los robots de montaje. Las AOI en el sistema en línea se han configurado de tal manera que registran hasta la más mínima divergencia. Y después del montaje THT, los módulos vuelven a someterse a prueba. Al realizar la comprobación final del equipo completo también se prueban las interfaces de E/S analógicas y digitales y a continuación se lleva a cabo un ensayo final de rendimiento a plena carga. Todas las pruebas se ejecutan a partir de la configuración individual del cliente. Así se consigue una seguridad adicional, es posible visualizar las instrucciones de montaje y se graban los equipos a láser. Esta es la única forma de garantizar la elevada calidad y fiabilidad de los productos NORD. La fabricación del equipo descentralizado NORDAC LINK en Aurich demuestra que en NORD DRIVESYSTEMS no hacemos concesión alguna, ni siquiera en la propia producción. Hace tiempo que en nuestras plantas de producción apostamos por la digitalización, la automatización y la mayor flexibilidad posible durante la fabricación de los variadores de frecuencia.