Wie ein Frequenzumrichter entsteht: Blick hinter die Kulissen in Aurich
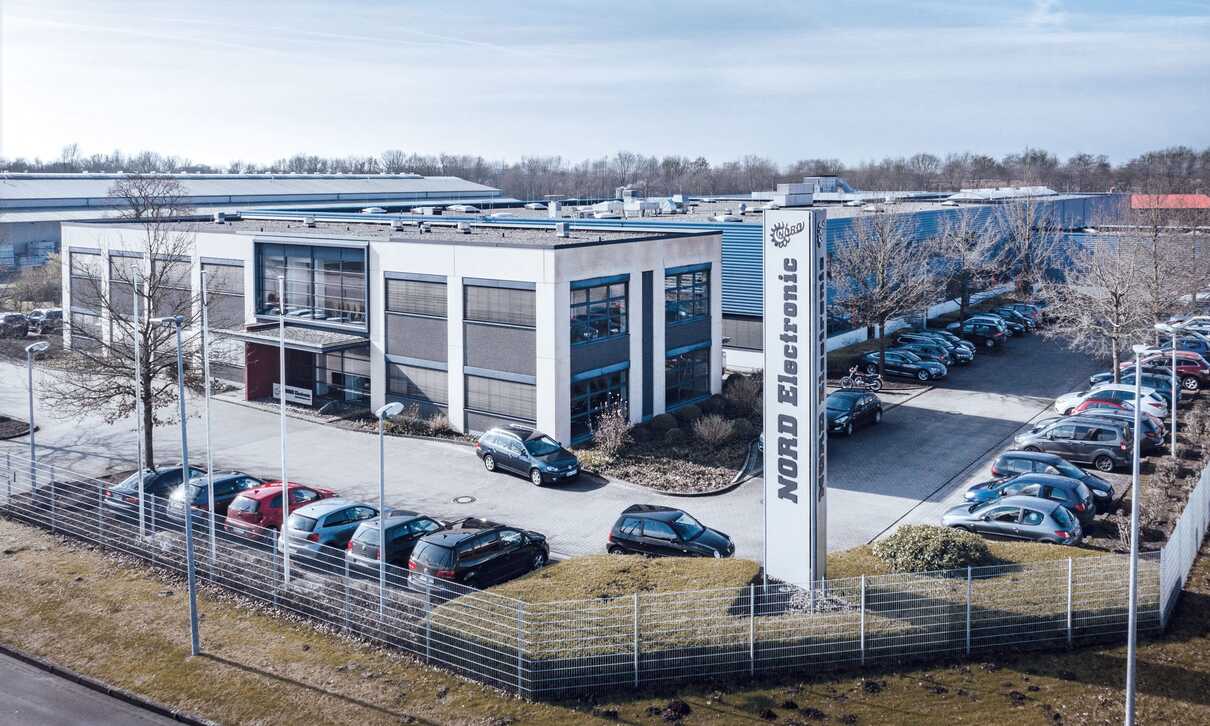
Die Zeiten der industriellen Massenproduktion mit wenigen Produktvarianten und hohen Stückzahlen sind längst passé. Individualität ist heute gefragter denn je. Die Kunden fordern zunehmend spezifische Konfigurationen, die exakt auf ihre individuellen Bedürfnisse zugeschnitten sind. Und dieser Megatrend wird sich in Zukunft ungebrochen fortsetzen. Zugleich werden immer kleinere Produktchargen verlangt. Diese steigende Varianz bei sinkenden Losgrößen ist mit herkömmlichen Fabrikstrukturen nicht zu bewältigen. Um schnell und flexibel auf Kundenwünsche und Marktveränderungen reagieren zu können, braucht es intelligente, wandelbare und effiziente Fertigungsverfahren. Industrie 4.0, die smarte vollvernetzte Produktion, liefert hier die Antwort.
Egal ob sie in Europa, China oder den USA zum Einsatz kommen, die Wiege eines jeden NORD-Frequenzumrichters – ob Schaltschrankumrichter oder dezentraler Frequenzumrichter – ist das NORD-Fertigungswerk in Aurich, Ostfriesland. Seit Anfang der 1980er Jahre unterhält NORD DRIVESYSTEMS, einer der weltweit führenden Komplettanbieter elektrischer, mechanischer und elektronischer Antriebstechnik, im Nordwesten Niedersachsens eine eigene Elektronikfertigung. Im Laufe der Jahre haben wir unser Portfolio und den Standort kontinuierlich ausgebaut. Heute beschäftigen wir bei der dortigen NORD Electronic DRIVESYSTEMS GmbH 180 Mitarbeiter (plus weitere 40 Mitarbeiter in der Entwicklung) und haben im Jahr 2022 185.000 Einheiten produziert, Tendenz steigend. Die Produktionsfläche beträgt 7.000 m2 und die Bürofläche 1.300 m2. Das Angebot umfasst dabei elektronische Antriebstechnik bis 160 kW (Umrichter, Motorstarter und Elektronik). Für den Start der Serienproduktion des Frequenzumrichters NORDAC LINK wurde im Zuge der Werkserweiterung eigens eine neue Montagelinie in Betrieb genommen.
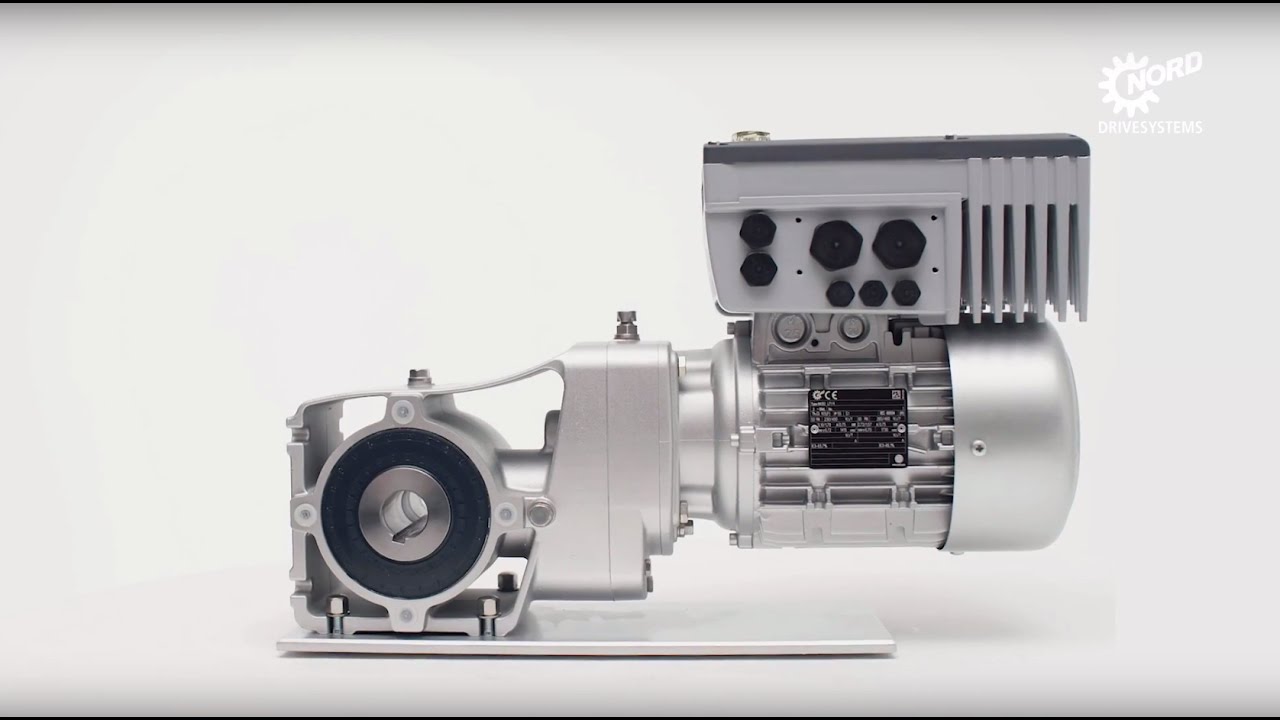
Auch die neueste Generation der NORDAC PRO-Frequenzumrichter für den Schaltschrankeinbau produzieren wir in Aurich auf dem neuesten Stand der Fertigungstechnik und -logistik. Besonders die Nachfrage nach kundenindividuell konfigurierten Geräten ist in den letzten Jahren massiv angestiegen. Deshalb haben wir weiter in den Standort Aurich investiert und die Kapazitäten mit einem finanziellen Aufwand von etwa 2,5 Millionen Euro deutlich vergrößert: Die Fläche für die Montage von Kundenprojekten ist auf 3.000 Quadratmeter gewachsen, verteilt auf zwei Etagen. Die Fertigungskapazität liegt jetzt bei 400.000 Einheiten – also Frequenzumrichter jeglicher Bauart. Der Zukauf eines Nachbargrundstücks mit einer Fläche von 1,8 ha sichert den weiteren Ausbau am Standort Aurich.
Schlanke Logistik – effiziente Prozesse
Ausschlaggebend für die Entwicklung des NORDAC LINK und unser verstärktes Engagement für eine State-of-the-Art-Fertigung in der Antriebselektronik war die voranschreitende Digitalisierung, Flexibilisierung und Individualisierung in der Industrie. Der Trend geht hin zu kundenspezifischen Bestellungen, kleineren Losgrößen und dezentralen Geräten. Moderne Antriebstechnik muss flexibel und individualisierbar sein und sich in alle Anlagen und Systeme problemlos integrieren lassen. Mit dem NORDAC LINK – und selbstverständlich allen anderen neuen Frequenzumrichter-Serien – tragen wir dieser Entwicklung Rechnung.
Die Baureihe wurde speziell für Anwendungen in modernen vernetzten Intralogistikanlagen entwickelt und bietet eine komfortable Antriebslösung für die flexible dezentrale Installation. Dank integrierter PLC können die effizienten Frequenzumrichter komplette Ablaufsteuerungen übernehmen und Prozesse autark regeln. Alle Module, Bauteile und Anschlüsse werden beim NORDAC LINKüber einfache Steckverbindungen zusammengefügt. Zusätzlich zur hohen Steckbarkeit sorgen optional integrierte Wartungsschalter und Handbedienschalter für eine hohe Benutzerfreundlichkeit. Der Frequenzumrichter ist für jede Anforderung und Anwendung frei konfigurierbar und mit allen marktüblichen Bussystemen kompatibel. Damit bietet er dem Kunden deutlich mehr Möglichkeiten zur Individualisierung als bisherige Produkte. Das hat natürlich auch Auswirkungen auf die Herstellung. Ziel bei der Planung der Produktionsprozesse für den NORDAC LINK war es, alle erforderlichen Montage- und Testsysteme anhand der individuellen Konfiguration zu steuern. Diese Strategie wurde vom Erzeugen des Bestückungsplans für die Bauteilebestückung bis hin zur Endprüfung und Parametrierung erfolgreich umgesetzt.
Von der Leiterplatte bis zum fertigen Frequemzumrichter
Die automatisierte und flexible Produktionsstruktur in Aurich ist technisch auf dem neusten Stand und erlaubt es, jede Auftragsgröße gleichermaßen auszuführen. Auch kleine Losgrößen sind dank der flexiblen Produktion möglich. Der NORDAC LINK wird direkt auf Kundenauftrag produziert. Er wird in SAP auf Baugruppenebene konfiguriert und dann auftragsbezogen bestückt und montiert. Dadurch hat der Kunde die Möglichkeit, deutlich mehr Merkmale zu konfigurieren. Auch für den Produktionsprozess ergeben sich Vorteile: Die komplette Fertigung wird über einen zentralen Auftrag gesteuert. Alle Daten und Informationen sind online gebündelt und lassen sich jederzeit überall abrufen. So werden unter anderem die Bestück- und Prüfpläne automatisch aus der individuellen Konfiguration erstellt, und zwar in der THT-Fertigung genauso wie im SMD-Bereich (Surface Mounted Device). Das ist ein Novum in der Baugruppenbestückung. Anhand eines QR-Codes auf der Baugruppe können in der THT-Bestückung die Arbeitspläne an den einzelnen Stationen angezeigt werden. Das stellt nicht nur sicher, dass das richtige Bauteil in das richtige Gerät eingesetzt wird, sondern ermöglicht auch eine größere Flexibilität. Für mehr Effizienz sorgt auch ein autonomes führerloses Transportsystem (FTS), das zum Beispiel für den Transport von der Warenannahme bis zum automatischen Kleinteilelager (AKL) zuständig ist und sukzessive weitere Routen übernehmen wird.
Bereits am Wareneingang beginnt der effiziente Prozess. Um möglichst wenig Verpackung in die Fertigung zu bringen, wird jedes Packstück von der Umverpackung befreit und in Standardboxen umgelagert. Den nachgeschalteten Transport erledigt das FTS. Außerdem erhält die Ware einen 2D-Code und kann so bis zur Verwendung lückenlos verfolgt werden bzw. auch umgekehrt von der Seriennummer des Gerätes bis zum Wareneingang.
Dreh- und Angelpunkt ist das automatische Kleinteilelager. Das AKL verfügt über 2.000 sechsfach segmentierte Standardboxen und ist zentral in die Produktionsabläufe integriert. Es dient nicht nur als Komponentenlager, sondern auch für halbfertige Produkte und zur Verkettung der Produktionsabläufe. Nach dem SMD-Bereich gehen die bestückten Baugruppen wieder zurück ins AKL und werden von dort für die weitere THT-Bearbeitung entnommen. So wird ein automatisches FIFO-Verfahren (First in, First out) innerhalb des Produktionsprozesses realisiert.
In der SMD-Fertigung erreichen die zwei Bestückungslinien in Spitzenleistung eine Kapazität von 60.000 Teilen pro Stunde. Um eine fehlerfreie Herstellung sicherzustellen, werden alle Baugruppen nach dem Bestücken und der Lötung unter Stickstoffatmosphäre mittels eines Inline-AOI-Systems (automatische optische Inspektion) kontrolliert. In der THT-Fertigung werden die bedrahteten Komponenten bestückt und mit Wellenlötanlagen unter Stickstoffatmosphäre gelötet. Je nach Komplexität erfolgt eine THT-AOI-Prüfung und ein sich anschließender 100%-Funktionstest. Von der THT-Fertigung geht es direkt weiter in das Kanban-Lager der Endmontage. Da alle Produkte auf Kundenauftrag produziert werden, bedarf es nur eines geringen Produktionsvorlaufs und kleiner Lagerkapazitäten.
An unserem NORD-Stammsitz in Bargteheide kommen die einzelnen Geräte – Getriebe, Motor und Umrichter – aus den unterschiedlichen Produktionsstätten zusammen und werden zu einer kompletten Antriebslösung vereint. Als Logistikhub verfügt NORD DRIVESYSTEMS Bargteheide über 34.000 Lagerplätze, davon 17.000 im Hochregallager. Mit einem neuen automatischen Kleinteilelager (AKL) mit mehr als 70.000 Plätzen ist 2021 noch das größte automatische Lagersystem der NORD DRIVESYSTEMS-Gruppe hinzugekommen. Neben dem AKL befindet sich in den neuen Hallen auch ein Schmalganglager mit 4.400 Palettenplätzen sowie ein Wareneingangs- und Versandbereich. Die Teileverpackung ist jetzt ebenfalls dort angesiedelt. So können wir unsere Kunden und Tochterunternehmen künftig noch schneller mit Frequenzumrichtern, Getriebeeinheiten und Motoren beliefern. Durch die höhere Verfügbarkeit vieler Komponenten verkürzen sich zudem die Montagezeiten am Standort Bargteheide.
Fehlerquellen ausschließen, Qualitätsstandards halten
Vor dem Weg in die norddeutsche Antriebstechnikzentrale müssen die Frequenzumrichter aber die vom Markt geforderten hohen Qualitätsstandards erfüllen. Um die abzusichern, sind in Aurich in allen Fertigungsstufen entsprechende Qualitätskontrollen integriert. Das fängt mit Bauteilkontrollen im Wareneingang an und setzt sich bei der Aufrüstung der Bestückungsautomaten fort. Der AOI-Test im Inline-System ist so eingestellt, dass bereits geringste Abweichungen registriert werden. Auch nach der THT-Fertigung werden alle Baugruppen noch einmal getestet. Bei der Endprüfung der kompletten Geräte erfolgt die finale Prüfung aller analogen und digitalen I/O-Schnittstellen sowie ein abschließender Leistungstest unter Volllast. Alle Tests werden anhand der individuellen Konfiguration durchgeführt. Das sorgt für zusätzliche Sicherheit, ebenso wie die Visualisierung der Montageanleitungen und die Laserbeschriftung der Geräte. Nur so kann die hohe Qualität und Zuverlässigkeit der NORD-Produkte gewährleistet werden. Die Herstellung des NORDAC LINK-Frequenzumrichters in Aurich zeigt: Auch bei der eigenen Fertigung machen wir bei NORD DRIVESYSTEMS keine Kompromisse. Längst haben Digitalisierung, Automatisierung und größtmögliche Flexibilität bei der Frequenzumrichterfertigung Einzug in die Werkshallen gehalten.